Aluminum alloy is an alloy primarily composed of aluminum as the base metal with the addition of certain amounts of other alloying elements. The main alloying elements include copper, silicon, magnesium, zinc, and manganese, while the secondary alloying elements include nickel, iron, titanium, chromium, lithium, and others.
Aluminum alloys have a low density (approximately 2.63-2.85 g/cm3) but relatively high strength (tensile strength σb ranging from 110 to 650 MPa), approaching that of high-alloy steels.
Aluminum alloys exhibit excellent castability and ductility, making them suitable for various profile shapes. They also possess excellent electrical conductivity, thermal conductivity, and corrosion resistance. Widely used in industries, aluminum alloys are the second most utilized material after steel.
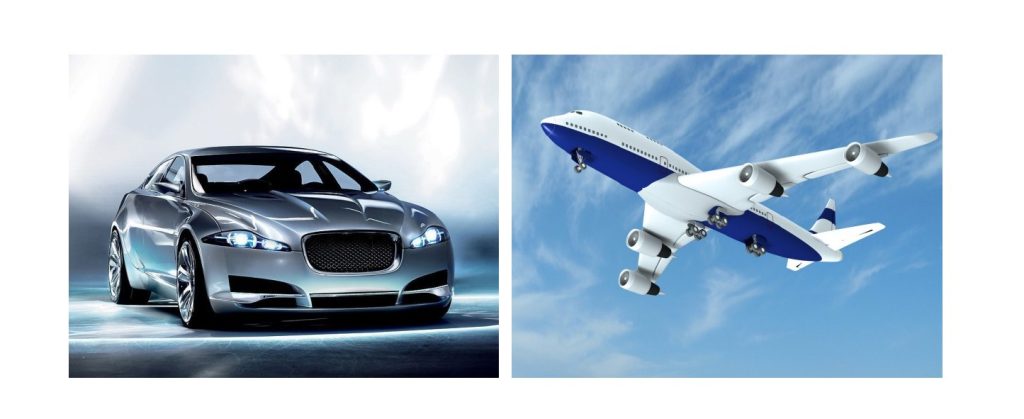
Aluminum alloys can be classified into two categories based on their composition and processing methods: wrought aluminum alloys and cast aluminum alloys.
Wrought Aluminum Alloys:
Wrought aluminum alloys are produced by melting the alloy ingredients and then subjecting them to plastic deformation processes, such as rolling, extrusion, stretching, and forging, to obtain various products through plastic processing.
Cast Aluminum Alloys:
Cast aluminum alloys are produced by melting the ingredients and directly casting them into various component blanks using methods such as sand casting, die casting, investment casting, and squeeze casting.
There are numerous standard material grades for aluminum and aluminum alloys. The commonly used series of grades are as follows:
1000 Series
Aluminum (Pure Aluminum)
Characteristics:
Aluminum content of 99.00% or higher. Relatively soft with low strength. Good formability and surface treatment. Good electrical conductivity and corrosion resistance. Excellent welding properties. Not suitable for heat treatment strengthening.
Application Range:
Mainly used in lighting fixtures, reflectors, decorations, chemical industry containers, heat sinks, welding wires, conductive materials, and special applications.
Typical Grades:
1050
Aluminum content of 99.5% or higher. Used for extruded tubes in the food, chemical, and brewing industries.
1060
Aluminum content of 99.6% or higher. Used in applications that require high corrosion resistance and formability but do not require high strength. Also used as a conductive material.
1085
Good formability and surface treatment. Excellent corrosion resistance. Can be used as a mirror finish aluminum in mobile phone components.
1100
Used for parts that require good formability, high corrosion resistance, but not high strength.
1N00
Slightly higher strength than 1100. Good formability. Similar characteristics to 1100.
1145
Used for packaging and insulation aluminum foil, heat exchangers.
1199
Used for electrolytic capacitor foils and optical reflective deposition films.
1350
Used for wires, stranded conductors, busbars, and transformer strips.
2000 Series
Al-Cu
Aluminum-Copper Alloys
Characteristics:
Aluminum alloys with copper as the main alloying element. Additional elements such as manganese, magnesium, lead, and bismuth may be added to improve machinability and hardness. High hardness but prone to intergranular corrosion. Relatively poor corrosion resistance.
Application Range:
Aerospace industry (2014 alloy). Screws (2011 alloy). Industries with high operating temperatures (2017 alloy).
Typical Grades:
2011
Fast machining alloy with good machinability and high strength but poor corrosion resistance.
2014
High copper (Cu) content. Used in aerospace industry. High strength and suitable for structural components.
2017
Slightly lower strength than 2014 but easier to process. Mainly used for rivets, general mechanical parts, structural components in transportation equipment, propellers, and accessories.
2024
Used in aircraft structures, rivets, missile components, truck wheel hubs, propeller elements, and other structural parts.
2025
Aluminum alloy for forging. Good forgeability and high strength but poor corrosion resistance. Used for propellers and magnetic drums.
2036
Used for automotive body sheet metal parts.
2048
Structural components for aerospace vehicles and weapon parts.
2117
After solution heat treatment, used as hinge pin material. Aluminum alloy with delayed room temperature aging speed.
2124
Structural components for aerospace vehicles.
2218
Aluminum alloy for forging. Good forgeability and high-temperature strength. Suitable for heat-resistant forging parts. Relatively poor corrosion resistance. Used for aircraft engine and diesel engine pistons, jet engine blades, and compressor rings.
2219
High-strength aluminum sheet with good low and high-temperature characteristics. Good weldability but poor corrosion resistance. Used for low-temperature containers and aerospace equipment parts.
2618
Aluminum alloy for forging. Superior high-temperature strength but poor corrosion resistance. Used for pistons, rubber forming molds, and components for general heat-resistant applications.
2A10
Higher strength than 2A01 alloy. Used for manufacturing aircraft structural rivets with working temperatures less than or equal to 100°C.
2A11
Medium-strength structural components for aircraft, propeller blades, transportation vehicles, and building structural components. Medium-strength bolts and rivets for aircraft.
2A12
Aircraft skin, bulkheads, ribs, wing beams, and rivets. Structural components for construction and transportation vehicles.
2A14
Complex-shaped free forgings and die forgings.
2A16
Aerospace components operating at temperatures of 250-300°C. Welding containers and airtight cabins operating at room temperature and high temperatures.
2A17
Aerospace components operating at temperatures of 225-250°C.
2A50
Complex-shaped medium-strength parts.
2A60
Aircraft engine compressor wheels, guide wheels, fans, impellers, etc.
2A70
Aircraft skin, aircraft engine pistons, guide wheels, wheels, etc.
2A80
Blades, impellers, pistons, expanders, and other high-temperature parts for aviation engines.
2A90
Aircraft engine pistons.
2N01
Aluminum alloy for forging. High strength and good heat resistance but poor corrosion resistance. Used for aircraft engines and hydraulic components.
3000 Series
Al-Mn
Aluminum-Manganese Alloys
Characteristics:
Aluminum alloys with manganese as the main alloying element. Cannot be heat treated for strengthening. Good corrosion resistance, often referred to as rust-proof aluminum. Good weldability and ductility. Lower strength, but strength can be enhanced through cold working. Susceptible to coarse grain formation during annealing.
Typical Grades:
3003
Approximately 10% higher strength than 1100 alloy. Good formability, weldability, and corrosion resistance. Used for seamless oil conduits in aircraft.
3004
Used for aluminum beverage can bodies. Requires higher strength than 3003 alloy for certain components. Used in chemical product production and storage devices, thin sheet processing parts, construction processing parts, construction tools, and various lighting components.
3005
Approximately 20% higher strength than 3003 alloy. Good corrosion resistance. Used for building materials and colored aluminum plates.
3105
Slightly higher strength than 3003 alloy. Used for room dividers, partitions, mobile home panels, eaves troughs, downspouts, thin sheet forming parts, bottle caps, and closures.
3A21
Used in aircraft fuel tanks, oil pipeline conduits, rivet wires, construction materials, industrial equipment for food production, etc.
4000 Series
Al-Si
Aluminum-Silicon Alloys
Characteristics:
Aluminum alloys with silicon as the main alloying element. Higher silicon content leads to higher strength. Some alloys within the 4xxx series can be heat treated for strengthening, while others cannot.
Typical Grades:
4032
Good heat resistance and wear resistance. Low coefficient of thermal expansion. Used for pistons and cylinder heads.
4043
Aluminum alloy for welding. Minimal solidification shrinkage. Naturally gray color after sulfuric acid anodizing treatment. Used for welding wires and architectural panels.
4343
Aluminum alloy for welding. Slightly higher silicon content than 4043. Low melting point, narrow solidification range, and good fluidity. Helps reduce shrinkage and minimize cracking during weld solidification. Used as clad layers for composite brazing plates.
5000 Series
Al-Mg
Aluminum-Magnesium Alloys
Characteristics:
Aluminum alloys with magnesium as the main alloying element. Low density, high tensile strength, high elongation, good corrosion resistance, good weldability, and good fatigue strength. Cannot be heat treated for strengthening, but strength can be improved through cold working.
Applications:
Lawn mower handles, aircraft fuel tank conduits, bulletproof vests.
Typical Grades:
5005
Similar strength to 3003 aluminum. Good workability, weldability, and corrosion resistance. Suitable for interior and exterior architectural applications, vehicle interiors, ship interiors, cookware, instrument panels, etc.
5052
Representative aluminum alloy with moderate strength. Good corrosion resistance, weldability, and formability. Particularly high fatigue strength and excellent resistance to seawater corrosion. Commonly used in manufacturing aircraft and automotive fuel tanks, pipes, sheet metal components for transportation vehicles and ships, instruments, streetlight brackets, hardware products, electrical enclosures, etc.
5056
Good anodizing and dyeing properties. Used for magnesium alloy rivets, zippers, nails, etc. Aluminum-clad wire widely used for processing agricultural insect traps and other applications requiring high corrosion resistance.
5083
Used in applications requiring high corrosion resistance, good weldability, and moderate strength. Examples include shipbuilding, automotive and aircraft panel welding components, pressure vessels requiring strict fire protection, refrigeration equipment, TV towers, drilling equipment, transportation equipment, missile components, armor, etc.
5086
Used in applications requiring high corrosion resistance, good weldability, and moderate strength. Examples include ships, automobiles, airplanes, low-temperature equipment, TV towers, drilling rigs, transportation equipment, missile components, decks, etc.
5154
Approximately 20% higher strength than 5052 with similar characteristics. Used for welded structures, storage tanks, pressure vessels, ship structures, offshore facilities, and transport tanks.
5182
Approximately 5% higher strength than 5083. Thin sheets used for processing beverage can lids, automotive body panels, steering wheels, reinforcements, brackets, etc.
5252
Used for manufacturing decorative components with higher strength, such as decorative parts for automobiles. After anodizing, it exhibits a bright and transparent oxide film.
5254
Used for hydrogen peroxide and other chemical product containers.
5356
Aluminum-magnesium alloy welding rod and wire with magnesium content greater than 3%.
5454
Used for welded structures, pressure vessels, and marine facility pipelines.
5456
Used for armor plates, high-strength welded structures, storage tanks, pressure vessels, and ship materials.
5457
Polished and anodized decorative parts for automobiles and other equipment.
5652
Storage containers for hydrogen peroxide and other chemical products.
5657
Polished and anodized decorative parts for automobiles and other equipment, with a requirement for fine grain structure in all cases.
5754
Moderate strength with good corrosion resistance, weldability, and formability. Mainly used for car doors, molds, gaskets, storage tanks, pressure vessels, ship structural components, etc.
5A02
Aircraft fuel tanks and conduits, welding wires, rivets, ship structural components.
5A03
Moderate strength welded structures, cold-stamped parts, welding containers, welding wires, can be used as a substitute for 5A02 alloy.
5A05
Welded structural components, aircraft skin frames.
5A06
Welded structures, cold die forgings, weld-pulled container load-bearing parts, aircraft skin bone components.
5A12
Welded structural components, bulletproof plates.
5N01
Same strength as 3003, good formability, and corrosion resistance.
5N02
Aluminum alloy for hinges, with good resistance to seawater corrosion.
6000 Series
Al-Mg-Si
Aluminum-Magnesium-Silicon Alloys
Characteristics:
Main alloying elements are magnesium and silicon. Mg2Si is the main strengthening phase and the most widely used alloy. Moderate strength, good corrosion resistance, good weldability, good processability (easy extrusion), and good oxidation coloring properties.
Applications:
The most widely used alloy, used in transportation vehicles (such as car luggage racks, doors, windows, car bodies, heat sinks, electrical enclosures).
Typical Grades:
6005
Extruded profiles and pipes used for structural components requiring higher strength than 6063 alloy, such as ladders, TV antennas, etc.
6009
Automotive body panels.
6010
Thin sheets used in automotive bodies.
6061
Heat-treatable corrosion-resistant aluminum alloy. It has good formability, weldability, and machinability, with moderate strength. Mainly used in aircraft parts, camera parts, ship components, valve parts, various hardware and electronic components.
6063
Representative aluminum alloy for extrusion. Lower strength than 6061 but better extrudability, suitable for complex section shapes. It has good corrosion resistance and surface treatment properties. Used in architectural aluminum doors and windows, curtain wall frames, irrigation pipes, as well as extruded materials for vehicles, stands, furniture, grilles, etc.
6066
Forgings and welded structural extrusion materials.
6070
Heavy-duty welded structures and extrusion materials and pipes for the automotive industry.
6101
High-strength conductive materials used for high-strength rods for buses, conductors, and radiator materials.
6151
Good forgeability, used for forged crankshaft parts, machine parts, and production rings. Requires good forgeability, high strength, and good corrosion resistance.
6201
High-strength conductive rods and wires.
6205
Thick plates, pedals, and extruded parts resistant to high impact.
6262
High-stress threaded parts requiring better corrosion resistance than 2011 and 2017 alloys. Same strength as 6061. Used in camera bodies, oxidizer components, brake components, gas appliance components.
6351
Extruded structural components for vehicles, pipelines for water, petroleum, etc.
6463
Building and various appliance profiles, as well as automotive decorative parts with bright surfaces after anodizing.
6A02
Aircraft engine parts, complex-shaped forgings and die forgings.
6N01
Medium-strength extrusion aluminum alloy with good extrudability and quench hardening properties. Used for complex large thin-walled profiles with good corrosion resistance and weldability.
7000 Series
Al-Mg-Zn-Cu
Aluminum-Magnesium-Zinc-Copper Alloys
Characteristics:
Main alloying elements are zinc, with small additions of magnesium and copper. Belongs to the aerospace series and is a heat-treatable alloy. It is a super-hard aluminum alloy with good wear resistance and weldability but relatively poor corrosion resistance. The super-hard aluminum alloy approaches the hardness of steel. Extrusion speed is slower than 6000 series alloys, but it has good welding properties.
Applications:
Aerospace applications (aircraft load-bearing components, landing gear), rockets, propellers, aerospace spacecraft.
Typical Grades:
7003
Extruded aluminum alloy for welding structures. Slightly lower strength than 7N01 but better extrudability, suitable for thin-walled large profiles. Used for the outer rims of vehicle wheels.
7005
Extrusion material used for manufacturing welded structures that require high strength and high fracture toughness, such as trusses, members, containers for transportation vehicles, large heat exchangers, and components that cannot undergo solid fusion treatment after welding. Also used for manufacturing sports equipment such as tennis rackets and baseball bats.
7039
Cryogenic containers, low-temperature instruments and storage boxes, fire pressure equipment, military equipment, armor plates, missile devices.
7049
Parts that require the same static strength as 7079-T6 alloy but with high resistance to stress corrosion cracking, such as aircraft and missile parts (landing gear hydraulic cylinders and extrusions). The fatigue performance of the parts is roughly equivalent to 7075-T6 alloy, with slightly higher toughness.
7050
Aluminum alloy that improves the quenching characteristics of 7075, with good resistance to stress and corrosion cracking. Suitable for medium-thick plates, extrusions, free forgings, and die forgings used in aircraft structural components. The requirements for this type of parts are high resistance to exfoliation corrosion, stress corrosion cracking resistance, fracture toughness, and fatigue resistance.
7072
Low electrode potential, mainly used for corrosion-resistant cladding skin materials, also suitable for heat exchanger fins. Used for aluminum foil and ultra-thin strip materials for air conditioners. Also used as a cladding layer for 2219, 3003, 3004, 5050, 5052, 5154, 6061, 7075, 7475, and 7178 alloy sheets and tubes.
7075
One of the highest strength materials in aluminum alloys (tensile strength ≥560 MPa, hardness HB150, density 2.81 g/cm3). It has good mechanical properties and is used for manufacturing aircraft structures, high-stress structural components, molds, machinery and equipment, and tooling fixtures. It has relatively poor corrosion resistance and is often paired with 7072 as a cladding skin material to improve corrosion resistance.
7175
High-strength structural aluminum alloy for forging aerospace components. T736 material has excellent comprehensive properties, including high strength, resistance to exfoliation corrosion, stress corrosion cracking resistance, fracture toughness, and fatigue strength.
7178
High-strength components required for manufacturing aerospace vehicles.
7475
Clad and unclad sheets for aircraft fuselages, wing frames, stringers, etc. Also used for components that require both high strength and high fracture toughness.
7A04
Aircraft skin, screws, and structural components such as main beams, stringers, ribs, and landing gear.
7A09
Chinese standard grade for 7075 aluminum alloy.
7N01
Aluminum alloy for welding structures, with high strength and weld strength close to the base material, and good corrosion resistance.
8000 Series
Other Types of Aluminum Alloys
8011
Aluminum alloy with added Fe and Si elements, commonly used as aluminum foil material.
9000 Series
Reserved aluminum alloy grades.
Aluminum Alloy Material Grades and Status Codes
F – Free Processing State
Applicable to products with special requirements for work hardening and heat treatment conditions during the forming process. The mechanical properties of products in this state are not specified.
O – Annealed State
Applicable to processed products that have achieved the lowest strength through complete annealing.
O1
Material processed and then heated at approximately the same temperature as solution heat treatment for an equivalent time, followed by slow cooling to room temperature.
O2
A deformation treatment state used to improve the formability of the material through superplastic forming (SPF).
O3
State after uniformization treatment.
H – Work Hardened State
Applicable to products where strength is increased through work hardening. The product can undergo additional heat treatment (optional) to reduce strength (generally non-heat-treatable reinforced materials).
The first digit after H represents the method of work hardening treatment.
H1
Pure work hardening state. Applicable to products that achieve the required strength through work hardening without additional heat treatment.
H2
Work hardened and partially annealed state. Applicable to products that exceed the specified requirements for work hardening and undergo partial annealing to reduce strength to the specified level.
H3
Work hardened and stabilizing treatment state. Applicable to products where the mechanical properties stabilize through low-temperature heat treatment after work hardening or due to the heating effects during the processing.
H4
Work hardened and paint-treated state. Applicable to products that undergo paint treatment after work hardening, resulting in partial annealing.
The second digit after H represents the level of hardness achieved by the material.
Hardness is generally classified into eight levels, with 1 being the lowest and 8 being the highest. In special cases, 9 represents a super-hard state with higher work hardening.
H12
Work hardened to 25% hardness.
H14
Work hardened to 50% hardness.
H16
Work hardened to 75% hardness.
H18
Work hardened to 100% hardness. Fully hardened state.
H19
Super work hardened state. The tensile strength of this material should be more than 10N/mm2 higher than that of the H18 state.
H22
Work hardened and partially annealed to 25% hardness.
H24
Work hardened and partially annealed to 50% hardness.
H26
Work hardened and partially annealed to 75% hardness.
H28
Work hardened and partially annealed to 100% hardness.
H32
Work hardened and stabilized treatment to 25% hardness.
H34
Work hardened and stabilized treatment to 50% hardness.
H36
Work hardened and stabilized treatment to 75% hardness.
H38
Work hardened and stabilized treatment to 100% hardness.
H42
Work hardened and paint-treated, 25% hardness treatment.
H44
Work hardened and paint-treated, 50% hardness treatment.
H46
Work hardened and paint-treated, 75% hardness treatment.
H48
Work hardened and paint-treated, 100% hardness treatment.
H111
Applicable to products that have undergone final annealing and have been moderately work hardened but not to the extent of the H11 state.
H112
Applicable to products formed by hot working, with specified requirements for mechanical properties.
H116
Applicable to products made from 5000 series alloys with a magnesium content ≥4.0%. These products have specified requirements for mechanical properties and resistance to exfoliation corrosion.
W – Solid Solution Heat Treatment State
An unstable state applicable only to alloys that have undergone solid solution heat treatment and natural aging at room temperature. This state code indicates that the product is in the natural aging stage.
T Heat Treatment State
Unlike the F, O, and H states, it is applicable to products that have reached a stable state after heat treatment, with or without subsequent work hardening. The T code must be followed by one or more Arabic numerals (generally for heat-treated strengthening materials).
The digits 0-10 following T represent the heat treatment process for the product.
T0
After solution heat treatment, the product goes through natural aging and then undergoes cold working. It is suitable for products that have been cold worked to improve strength after solution heat treatment.
T1
The product is cooled after a high-temperature forming process and then naturally aged to a basically stable state. It is suitable for products that are cooled after a high-temperature forming process and no longer undergo cold working (can undergo straightening or flattening, but it does not affect the mechanical performance limits).
T2
The product is cooled after a high-temperature forming process and then undergoes cold working before being naturally aged to a basically stable state. It is suitable for products that are cooled after a high-temperature forming process and undergo cold working or straightening and flattening to improve strength.
T3
After solution heat treatment, the product undergoes cold working and then is naturally aged to a basically stable state. It is suitable for products that undergo cold working or straightening and flattening to improve strength after solution heat treatment.
T4
After solution heat treatment, the product is naturally aged to a basically stable state. It is suitable for products that, after solution heat treatment, no longer undergo cold working (can undergo straightening or flattening, but it does not affect the mechanical performance limits) and then undergo natural aging.
T5
The product is cooled after a high-temperature forming process and then artificially aged. It is suitable for products that are cooled after a high-temperature forming process and do not undergo cold working (can undergo straightening or flattening, but it does not affect the mechanical performance limits) and then undergo artificial aging.
T6
The product undergoes artificial aging after solution heat treatment. It is suitable for products that, after solution heat treatment, no longer undergo cold working (can undergo straightening or flattening, but it does not affect the mechanical performance limits) and then undergo artificial aging.
T7
The product undergoes artificial aging after solution heat treatment. It is suitable for products that, after solution heat treatment, surpass the peak strength point on the aging curve during artificial aging to obtain certain important characteristics.
T8
After solution heat treatment, the product undergoes cold working and then artificial aging. It is suitable for products that undergo cold working or straightening and flattening to improve product strength.
T9
After solution heat treatment, the product undergoes artificial aging and then cold working. It is suitable for products that undergo cold working to improve product strength.
T10
The product is cooled after a high-temperature forming process, undergoes cold working, and then undergoes artificial aging. It is suitable for products that undergo cold working or straightening and flattening to improve product strength.
For larger numbers following T, they represent specific process treatments that significantly change product characteristics such as mechanical properties and corrosion resistance.
T42
It is suitable for products that have reached a fully stable state after solution heat treatment from the O or F state and also for products that have undergone any state of machining and heat treatment, with mechanical properties reaching the T42 state.
T62
It is suitable for products that have undergone artificial aging after solution heat treatment from the O or F state and also for products that have undergone any state of machining and heat treatment, with mechanical properties reaching the T62 state.
T73
It is suitable for products that have undergone solution heat treatment and aging to achieve specified mechanical properties and stress corrosion resistance performance indicators.
T74
Same definition as the T73 state. The tensile strength of this state is higher than T73 but lower than T76.
T76
Same definition as the T73 state. The tensile strength of this state is higher than both T73 and T74, and the stress corrosion fracture resistance is lower than T73 and T74, but the delamination corrosion resistance is still good.
T7X2
It is suitable for products that have undergone artificial aging after solution heat treatment from the O or F state, with mechanical properties and corrosion resistance reaching the T7X state.
T81
It is suitable for products that have undergone solution heat treatment, followed by about 1% cold deformation to improve strength, and then artificial aging.
T87
It is suitable for products that have undergone solution heat treatment, followed by about 7% cold deformation to improve strength, and then artificial aging. Stress-relieved state.
TX followed by a number indicates the state of a product that has undergone stress relief treatment.
TX51 TXX51 TXXX51
Applicable to thick plates that have undergone solution heat treatment or cooled after a high-temperature forming process, with a specified amount of stretching; rolled or cold-finished bars that have been straightened; as well as die forgings, forged rings, or rolled rings that no longer undergo straightening after stretching.
The permanent deformation for thick plates is 1.5% to 3%.
The permanent deformation for rolled or cold-finished bars is 1% to 3%.
The permanent deformation for die forgings, forged rings, or rolled rings is 1% to 5%.
The permanent deformation for extruded rods, shapes, and tubes is 1% to 3%.
The permanent deformation for drawn tubes is 1.5% to 3%.
TX511 TXX511 TXXX511
Applicable to extruded rods, shapes, and tubes that have undergone solution heat treatment or cooled after a high-temperature forming process, with a specified amount of stretching; as well as drawn tubes, which can undergo slight straightening after stretching to meet standard tolerances.
TX52 TXX52 TXXX52
Applicable to products that have undergone solution heat treatment or cooled after a high-temperature forming process, and are subjected to compression to relieve stress, resulting in a permanent deformation of 1% to 5%.
TX54 TXX54 TXXX54
Applicable to die forgings where stress is relieved through cold sizing within the final forging die.