The cutting tool material used for cutting must have sufficient hardness (The basic requirement that the cutting material is harder than the workpiece material.), toughness (Needed to prevent breaking and crack formation. Is equivalent to the flexural strength of the material under the conditions that are present, together with its break resistance. Toughness is highly relevant to adhesive-wear resisitance.), and a certain level of hot hardness (Continued hardness at elevated temperatures) and chemical resistance (Ability to resist chemical precosses under the conditions present, including those of oxidation and the occurrence of diffusion processes.).
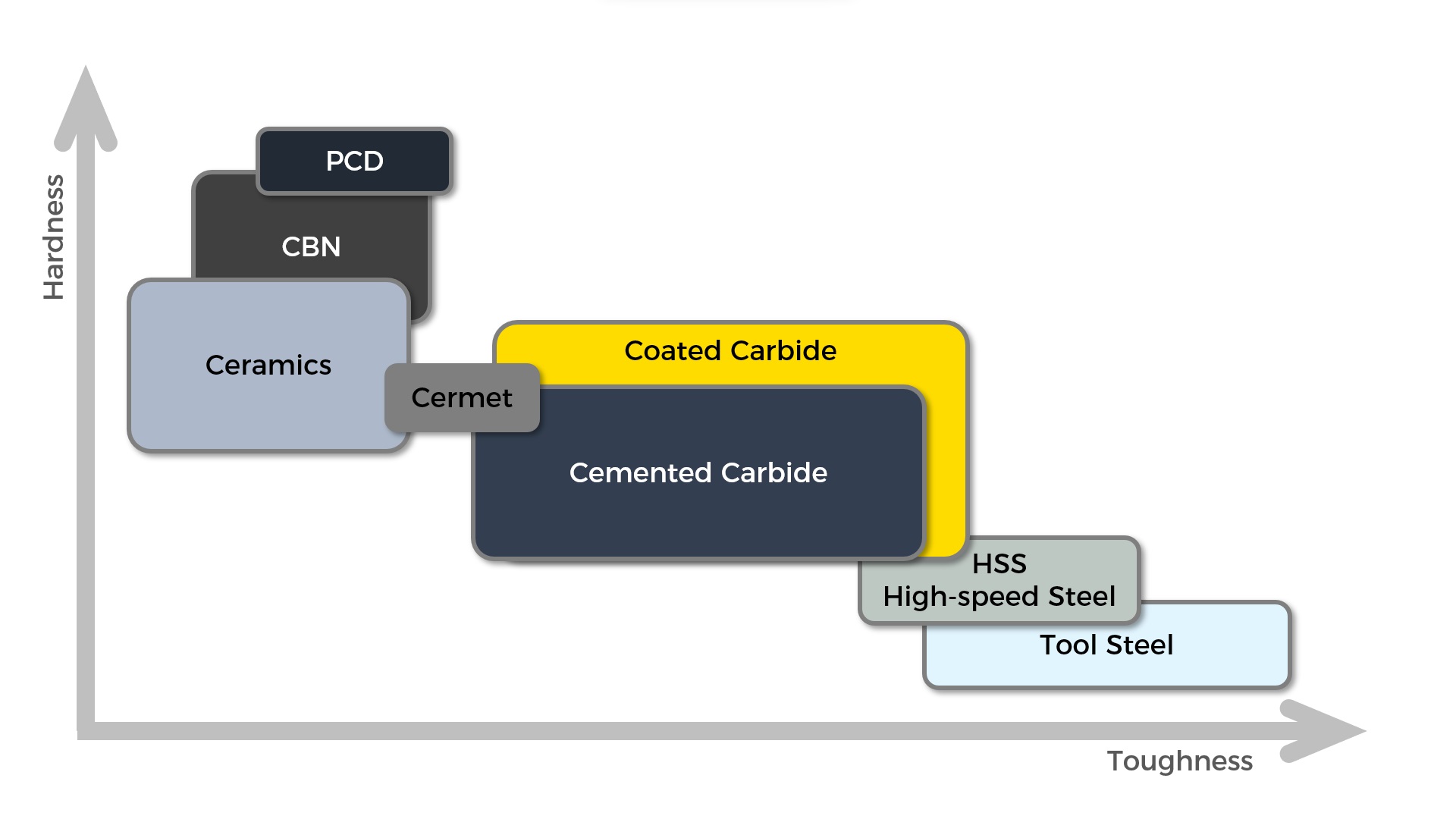
The main cutting tool materials include:
Tools Steel
The discovery of hardening methods for carbon steel, enabling it to cut unhardened carbon steel, marked a significant advancement in cutting tool material development. This led to the term “tool steel.” However, when used for metal cutting, it required very low cutting speeds. Without hot-hardening, it starts to soften around 200°C. Tool steel, in its current form, is a high-alloy steel primarily used in forming workpiece materials. It is categorized into three types: cold-working steel, hot-working steel, and die steel, depending on the application area. While tool steels have limited use for cutting metallic materials, they are extensively employed for cutting organic materials like wood.
Cold-working steel, often alloyed with carbon and carbide-forming elements like vanadium and molybdenum, is commonly used for forming or clipping sheet metal or ceramics at normal temperatures. This alloy ensures sufficient hardness and wear resistance, with a typical hardness range of 58-63 HRC. AISI D2 (SS 2310) serves as a representative cold-working steel, employed in low-speed tools such as threading dies and reamers.
Hot-working steels are utilized for elevated temperature applications, such as molds for die casting aluminum components. These steels have a working hardness of approximately 45-52 HRC, requiring lower carbon content (around 0.4-0.5%) compared to cold-working steels. Molybdenum or vanadium alloys are crucial to maintain their strength at high temperatures. AISI H13 (SS 2242), commonly used for tool shafts and milling cutters, exemplifies a typical hot-working steel.
With the development of modern materials for products, tool steel’s limited hardness and poor hot hardness make it unable to meet the processing requirements of modern materials. It is only retained for use in a small number of manual tools.
High-speed Steel (HSS)
High-speed steel, developed in the early 20th century, facilitated the production of metal-cutting tools with significantly higher material removal rates. Despite considerable advancements, it is worth noting that even after more than 100 years, only a fraction of metal-cutting operations involve the use of high-speed steel tools. The original high-speed steel introduced by Taylor in 1900 contained 1.8% carbon, 3.8% chromium, and 8% tungsten. The name “high-speed steel” (HSS) was derived from its superior material removal capabilities compared to carbon steel tools. Over time, high-speed steels were further developed and gradually enhanced. In the 1940s, molybdenum replaced tungsten as an alloy element. In the 1960s, the carbon content was increased, and cobalt was introduced as an additional alloy element in some high-speed steels. The 1970s saw the introduction of powder-based high-speed steels, offering improved toughness and grindability. In the 1980s, performance was further enhanced by applying coatings such as titanium nitride (TiN) or titanium carbonitride (TiCN) to the steels.
Cermented Carbide
It was known very early that tungsten carbide was one of the hardest carbides found. At the beginning of the last century companies producing electric light bulbs had access to pure tungsten or produced it themselves, and in many parts of the world the manufacture of tungsten carbide was carried on in collaboration with companies of this sort. It was discovered that iron powder could serve as a binding metal in the sintering of tungsten carbide, but iron was soon replaced here by cobalt, whereupon cemented carbide received the basic composition it still has today. At the Leipzig Trade Fair of 1926, the German corporation Krupp presented the first metal-cutting tools made of cemented carbide, the patent for which they had purchased from Osram.
Marked improvements in the performance of cemented-carbide cutting tools was achieved later through development of better manufacturing techniques, which led to greater purity of the material, more adequate tool geometries and use of coatings of different types. Most types of cemented carbide used in metal cutting today are provided with a hard, brittle, chemically resistant ceramic coating.
Cemented carbides represent a group of composite materials, powder-metallurgically manufactured, characterized by high wear resistance and a high level of hardness and strength. They usually consist of hard particles of one or more types sintered together by a relatively tough binding metal. The hard particles are primarily carbides, and carbonitrides can also be present. The hard components tend to be quite hard, often having a hardness of greater than HV 2000, but to be of limited toughness. All cemented carbides have tungsten carbide (WC) as their most important hard phase, but they often contain either carbides, carbonitrides or nitrides of titanium, niobium, vanadium or chromium as well.
Cobalt is the most usual binding metal employed, but both nickel and iron, as well as alloys of these, can also be present. The task the binding metal or metals fulfill is to provide the composite material greater toughness and a solid consistency without pores, so that a desirable combination of hardness, wear resistance and toughness can be achieved.
Coating
Currently, the majority of widely used hard alloys are coated hard alloys, and the coating can effectively enhance the cutting performance of tools.
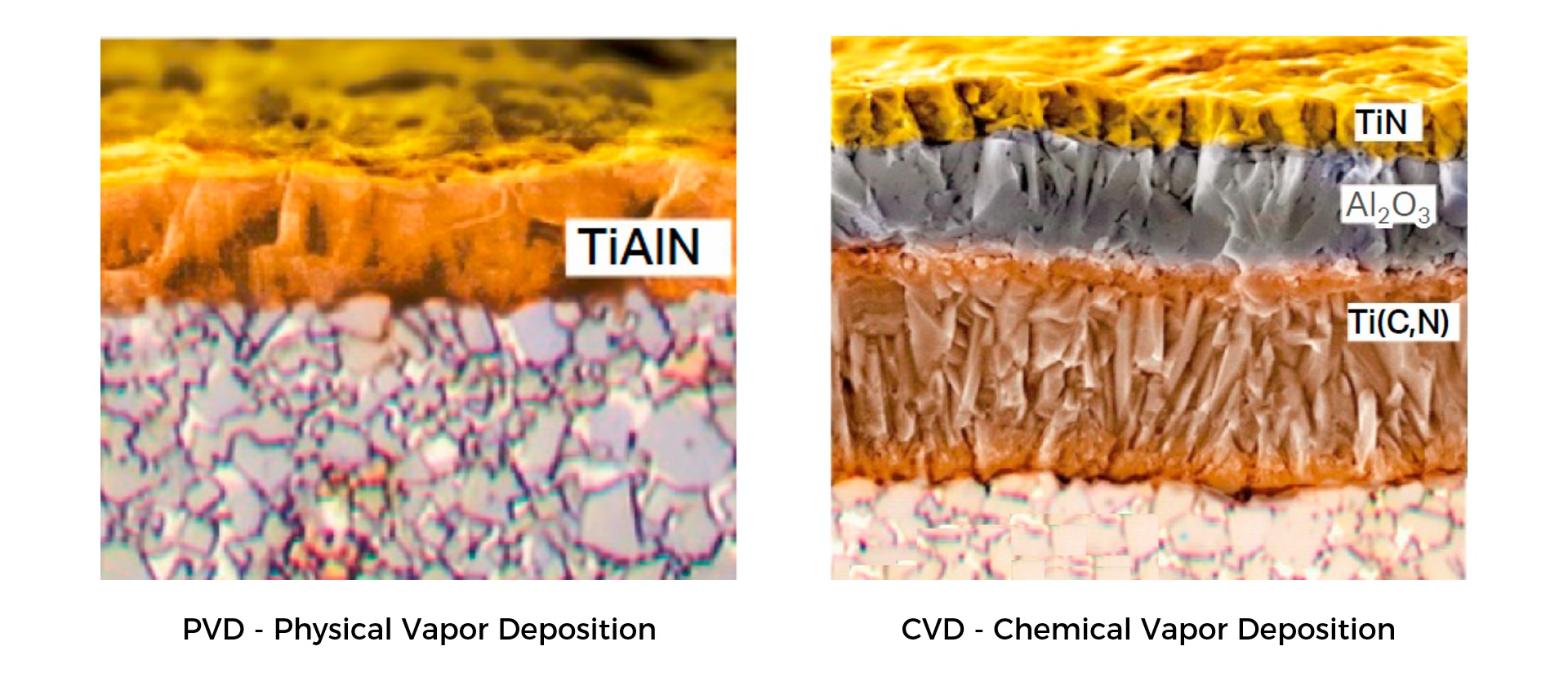
The coatings used to increase the wear resistance of the cutting edge usually consist of ceramics, although coatings of diamond or diamond-like substances are sometimes used. The ceramics employed include oxides, nitrides and carbides. Typical characteristics of ceramics are being stable at high temperatures, being chemically inert, being extremely hard and being brittle. Through the use of a thin coating of ceramics on cemented carbide or high-speed steel enables taking advantage of the positive characteristics that ceramics possess without needing to suffer from their brittleness.
The coating is 1 – 20 um thick, depending upon the application involved. A thin coating, 1 – 5 um thick, is applied using the PVD (Physical Vapor Deposition) technique, whereas the CVD (Chemical Vapor Deposition) technique is used for thicker (4 – 20 um) coatings.
The PVD-technique provides greater possibilities for varying the composition of the coating material, there being a large number of combinations of different materials that can be employed, yet the coatings most commonly used are those based on Ti, Al, Cr, Si, N, O and C. In use of the CVD-technique one can less readily vary the materials system employed. The major coating materials employed by the CVD technology today are TiC,N), TiN and Al03. However, since the first commercially made CVD-coatings the coating properties have been continuously refined and highly controlled. Current state of the art CVD coatings has proven that by controlling parameters such as stress state, phase composition and the orientation of the crystallites in the coating, especially in the Al203-coating, performance can be enhanced by orders of magnitude compared to previous CVD-coatings.
Cermet
Cermet is a type of cemented carbide that has Ni (nickel) as a binder and mainly TiC and TiN as hard components. Cermets are generally more brittle than other cemented carbides. They are used primarily in finishing operations so as to produce better surfaces.
Ceramics
Ceramics have been developed parallel to cemented carbides. They are exceedingly hard and can also withstand high temperatures very well. A disadvantage they have is their brittleness. The ceramic materials used for cutting tools most frequently are Al203 and SiN4 (silicon nitride). Only during about the last 15 years have ways been found to deal effectively with the brittle behavior of ceramics. Fiber reinforcement of them which has been introduced has led to marked improvement in their characteristics in this respect.
CBN
Cubic Boron Nitride (cBN) is a purely man-made superhard material not found in any form in nature.
Its unique properties, of extreme hardness (only diamond is harder), the ability to retain its hardness at elevated temperatures, and its inertness to iron, make cBN an ideal cutting tool material for the machining of hard and abrasive ferrous workpiece materials. Another superhard BN phase is the metastable wurtzite Boron Nitride (wBN), which has lesser hardness but possesses higher toughness, making it suitable for interrupted machining operations.
PCD
Diamond is the hardest, most wear resistant material in the world. Diamond tool materials are either polycrystalline or monocrystalline in character. Each class of diamond materials can be manufactured by either chemical vapor deposition (CVD) or ultra-high temperature and pressure synthesis. Polycrystalline diamond synthesized using ultra-high temperatures and pressures is the most popular form of diamond tool material. It is known universally by its abbreviation ‘PCD’. The diamond particles it contains, in the order 1-30 microns, are sintered together in the presence of a cobalt catalyst. The cobalt allows the PCD to be machined by electro discharge machining and toughened to a considerable degree, providing a more robust blank and increasing the ease of tool fabrication, the PCD being sintered directly on a tungsten carbide substrate.