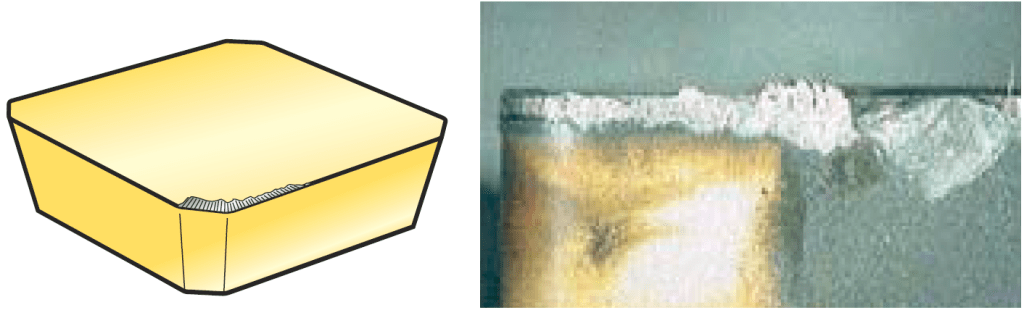
When cutting ductile materials within a certain cutting speed range, the workpiece material continuously accumulates and adheres near the cutting edge on the front face of the tool. In some cases, it may even weld onto the cutting edge of the tool, forming a built-up edge (BUE), commonly known as a “chip lump” or “tool lump.”
The formation of a built-up edge (BUE) can affect the relevant geometric parameters of cutting and alter cutting characteristics.
The material that forms the BUE is often much harder than the workpiece material itself. The BUE participates in the cutting process and provides a certain level of protection for the cutting edge.
The presence of a BUE causes actual changes in the radial and tangential positions of the cutting edge. It also alters the cutting angles. This, in turn, affects cutting forces, cutting heat, and chip formation. It can also impact the dimensional accuracy of the workpiece.
As the cutting process progresses, the built-up edge (BUE) continues to grow. When the accumulated BUE exceeds a critical size, it can fracture and detach under the impact and vibration of cutting forces. The detached BUE is then carried away by the chip flow or embedded on the workpiece surface. This cycle of BUE formation, fracture, and removal repeats throughout the entire cutting process. The presence of intermittent and varying-sized BUEs can lead to cutting vibrations, which can adversely affect machining quality.
The detached BUE may also carry away some tool material, ultimately leading to tool edge failure. Alternatively, it may remain on the machined surface, affecting the surface quality of the workpiece.
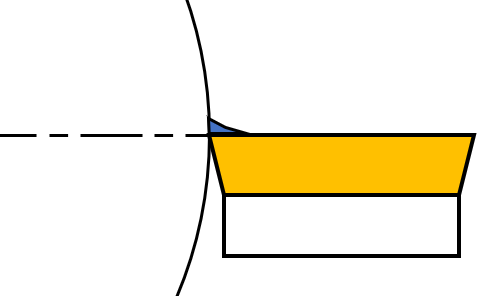
The formation of a built-up edge (BUE) is directly related to cutting temperature.
During the cutting process, due to metal deformation and intense friction, there is significant pressure and high cutting temperatures between the chip and the front face of the tool. When the pressure and temperature conditions are suitable, the frictional resistance between the chip base and the front face increases, causing the flow rate of the chip base to slow down, resulting in the formation of a thin “stagnation layer.” When the frictional resistance between the “stagnation layer” and the front face exceeds the internal cohesion of the chip, the metal of the “stagnation layer” separates from the chip and adheres near the cutting edge, forming a built-up edge. The formation of a built-up edge is essentially the result of cold welding during the cutting process.
The mechanism described above for the formation of a built-up edge is one of the explanations found in numerous related studies and provided for reference.
Key factors contributing to the formation of a built-up edge (BUE):
Cutting zone temperature:
The temperature in the cutting zone is the most critical factor in the formation of a BUE.
Cutting speed and chip thickness are key parameters that affect cutting temperature.
Adhesion characteristics between workpiece material and tool material:
The formation of a BUE is more likely when machining ductile materials such as low carbon steel, stainless steel, nickel-based alloys, aluminum alloys, etc.
The likelihood of BUE formation is lower when cutting brittle materials.
Geometric parameters of the tool:
For example, rake angle, relief angle, and cutting edge radius.
Increasing the rake angle of the tool can improve the friction between the chip and the front face, thereby suppressing the formation of a BUE or reducing its height.
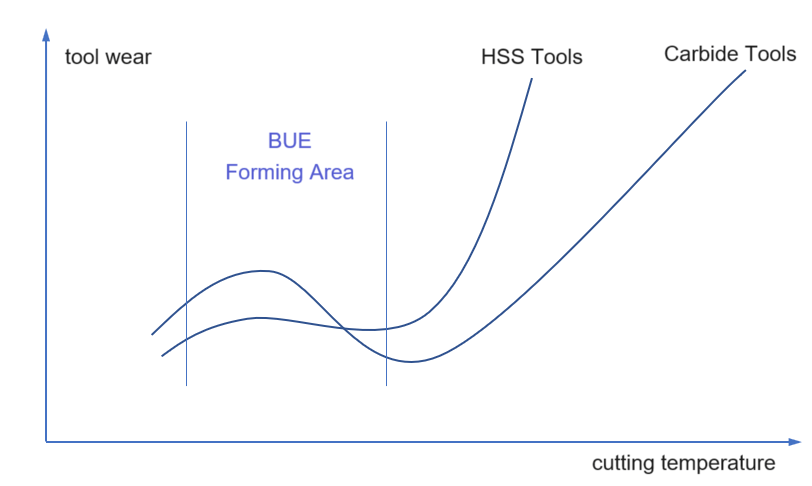
The impact of a built-up edge (BUE) on tool life:
When selecting cutting parameters and aiming for a better surface roughness, it is important to avoid cutting in the region where a built-up edge (BUE) is likely to form.
Improvement
Increasing cutting speed and feed rate (resulting in thicker chips) can both raise the cutting temperature, thereby helping to avoid the formation of a built-up edge (BUE) in the cutting zone.
Proper use of coolant or the absence of coolant can also increase the temperature in the cutting zone.
Choosing a tool material with poor adhesion to the workpiece material, particularly with the right coating, can be beneficial.
Selecting a sharper cutting edge is another effective approach.