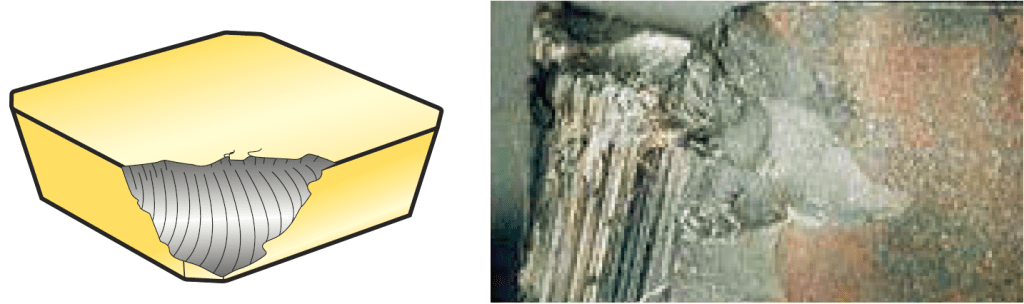
Insert breakage, distinct from tip fracture, refers to a larger-scale fracture that does not occur at the rounded corner of the tool tip.
The mechanism behind insert breakage is similar to tip fracture, as it is caused by excessive mechanical cutting loads.
Note:
In many cases, the gradual development of other types of wear can lead to a gradual increase in cutting loads. When the load exceeds a critical threshold, insert breakage can occur. In such cases, the first step is to examine the initial wear pattern to identify the cause and take appropriate measures to address it.
Insert breakages typically occur during tool entry, tool exit, or sudden changes in cutting conditions. They are often accompanied by a loud noise and immediate machine shutdown is necessary.
Note:
During the shutdown procedure, the first priority is to stop the feeding motion.
Conditions that are prone to insert breakage include:
- Fracture formed due to the continued development of other types of wear.
- Improper tool blade installation, unreliable fastening, uneven tool seat, or poor tool cushioning conditions.
- Inhomogeneous workpiece material with the presence of hard spots or porosity.
- Uneven cutting allowance on the workpiece, such as irregular castings or forged hard skins.
- Sudden changes in cutting allowance, such as corners in cavity machining.
- Poor system rigidity.
- Insufficient torque of the machine tool.
- Errors in programming paths, entering cutting while in rapid feed mode.
Improvement
Reduce the feed rate or cutting depth:
Effectively reduce the cutting load.
When entering or exiting the workpiece, or when encountering a sudden increase in cutting allowance, reduce the feed rate.
Inspect the system clamping conditions:
Check the tool clamping, workpiece clamping, machine tool rigidity, and other conditions.
Choose tool materials with good toughness:
To improve the tool’s impact resistance.
For inexperienced initial attempts, it is essential to select tool materials that are resistant to impact.
Select chip breaker designs suitable for rough machining:
To enhance cutting edge strength.
Choose thicker inserts:
To improve the tool’s resistance to impact.
Optimize programming paths:
Avoid problems caused by uneven cutting allowance or sudden changes in cutting allowance.
Pay attention to cutting torque:
Estimate cutting torque in advance, understand the machine tool’s torque limit, and avoid the phenomenon of “tool chatter.”
Important reminder:
This type of damage poses high risks, so pay attention to personal safety precautions!